Exactly How Welding Assessment Works: An Extensive Evaluation of Methods, Criteria, and the Duty of Assessors in Making Sure Structural Integrity and Safety And Security
Welding inspection is an essential part in the building and construction and production industries, where the honesty of bonded joints is vital to safety and integrity. Various approaches, including aesthetic and non-destructive screening methods, are employed to find possible problems that could jeopardize architectural performance - Houston Welding Inspection. Assessors are charged with not just assessing weld top quality against rigid standards yet also analyzing intricate codes and standards. As we check out the details of this profession, the challenges dealt with by examiners in maintaining security and compliance will certainly disclose a much deeper understanding of their important role in safeguarding infrastructure.
Significance of Welding Evaluation
Welding assessment is critical in making sure the honesty and safety of welded structures, with studies indicating that approximately 70% of architectural failures can be mapped back to inadequate welding methods. This underscores the value of methodical assessment procedures throughout the welding lifecycle, from preparation to conclusion. Efficient evaluation not just recognizes defects prior to they intensify into significant problems but additionally makes sure conformity with market criteria and regulations.

The role of welding inspectors extends past simple high quality control; they are essential in guarding public safety and minimizing responsibility for companies. By carrying out rigorous inspection procedures, firms can spot problems such as insufficient combination, fractures, or too much porosity, which can jeopardize the overall toughness of a welded joint. Additionally, recurring training and accreditation of inspectors add to the overall quality control in welding operations, promoting a culture of security and excellence.
Additionally, welding inspection plays a critical duty in keeping functional effectiveness. Determining flaws early at the same time facilitates prompt restorative activities, decreasing expensive rework and project hold-ups. Inevitably, a robust assessment structure works as a structure for long lasting and reliable welded frameworks, guaranteeing they satisfy both practical and safety and security demands.
Typical Examination Techniques
How can one ensure the top quality of welded joints throughout the evaluation process? The application of numerous examination approaches is important in examining weld honesty and recognizing possible defects. Common techniques consist of Visual Inspection (VT), which is usually the initial line of protection, permitting assessors to find surface area problems such as splits, porosity, or insufficient blend by aesthetically analyzing the welds.
Ultrasonic Checking (UT) is one more widely used technique, employing high-frequency sound waves to recognize internal defects within the weld. This method is specifically reliable for identifying concerns that are not noticeable to the nude eye. Radiographic Evaluating (RT) utilizes X-rays or gamma rays to create photos of the weld, making it possible for the recognition of volumetric problems, such as additions or voids.
Magnetic Fragment Checking (MT) and Liquid Penetrant Testing (PT) are additionally famous techniques, focusing on surface area issues. MT counts on magnetic areas to expose surface area and near-surface discontinuities, while PT entails using a liquid color to highlight problems. Each of these methods offers an unique purpose, ensuring the thorough analysis of welded joints and guarding structural honesty and security.
Requirements for Reviewing Welds
The examination of welds is guided by a collection of recognized criteria that guarantee both performance and safety in welded frameworks. These requirements incorporate numerous factors, consisting of weld size, account, and penetration, which must comply with specified criteria. Compliance with market codes, such as those established by the American Welding Society (AWS) or the American Society of Mechanical Engineers (ASME), is necessary in figuring out the reputation of a weld.
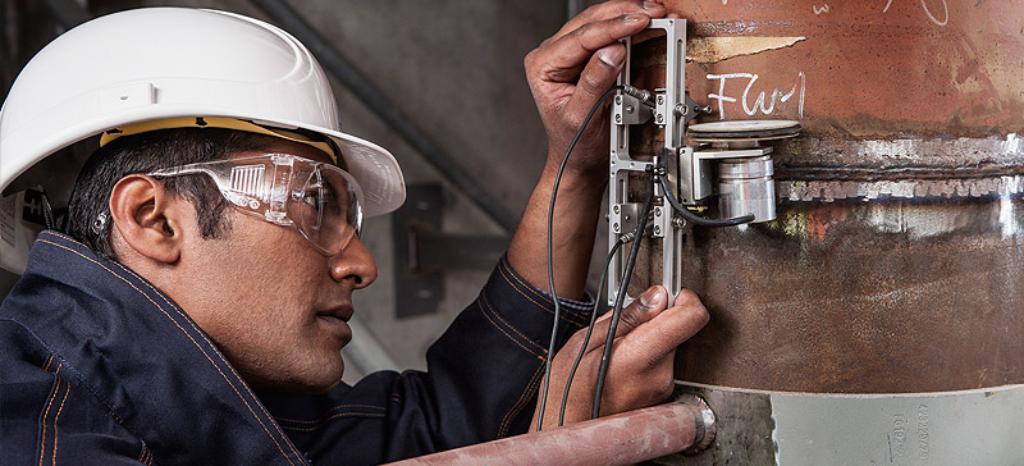
Weld metallurgy plays a crucial function; the examination takes into consideration the fusion high quality between base and filler materials, in addition to heat-affected areas. The overall mechanical homes, including tensile stamina and ductility, should fulfill the requirements developed for the particular application. Collectively, these criteria ensure that welds not just meet aesthetic criteria yet likewise carry out reliably under operational problems.
Duty of Welding Inspectors
A welding examiner's competence is critical in guaranteeing the integrity and quality of bonded structures. These professionals play an essential duty in the construction and building process by verifying that welding procedures stick to established criteria and specs. Their obligations include a detailed series of jobs, consisting of aesthetic examination of welds, evaluating welding documents, and performing non-destructive testing (NDT) techniques such as ultrasonic or radiographic screening to determine problems.
Welding assessors are additionally in charge of analyzing welding codes and standards, making certain that the welders are qualified which the materials made use of meet the essential requirements - Houston Welding Inspection. They have to keep precise documents of assessments, which function as paperwork of conformity and quality assurance. Additionally, these inspectors commonly collaborate with engineers and job supervisors to resolve any kind of concerns that emerge throughout the welding process, providing suggestions for rehabilitative activities when necessary.
In addition to technological skills, effective interaction is vital, as welding examiners have to convey findings plainly to stakeholders and facilitate training and directory advice for welders. Eventually, their duty is integral to maintaining safety and security and reliability in welded structures, contributing substantially to the total success of building projects.
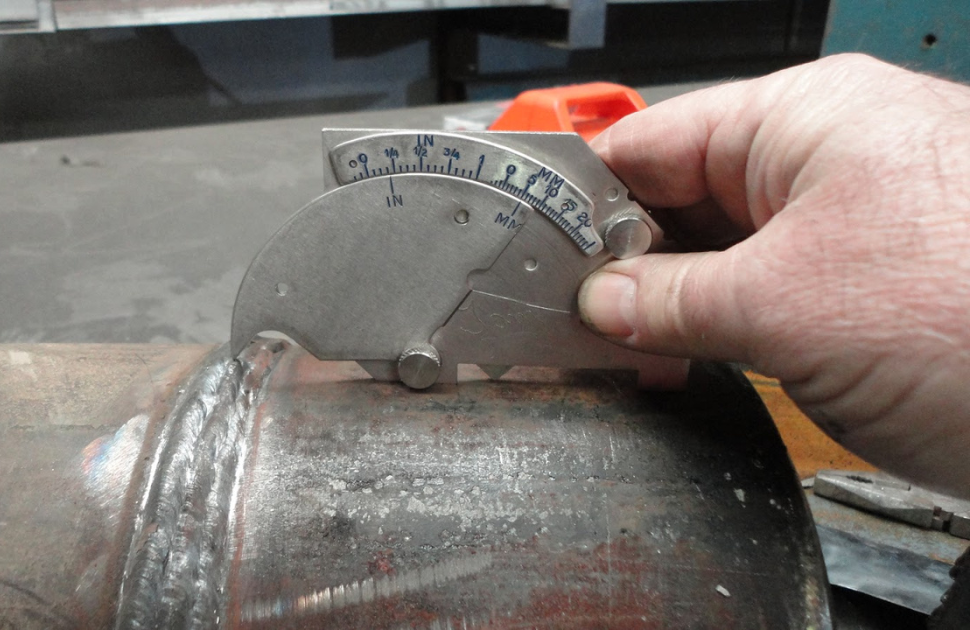
Obstacles in Welding Examination
What obstacles do welding assessors face in their essential function? The complexities of contemporary welding strategies and materials existing significant obstacles for great site inspectors entrusted with guaranteeing conformity with safety criteria and structural stability.
Additionally, examiners often run into variants in worksite problems that can prevent examination procedures. Factors such as ecological problems, ease of access, and the physical state of the bonded structures can make complex extensive evaluations. Time constraints imposed by task schedules can even more press assessors, potentially affecting the thoroughness of their evaluations.
In addition, the subjective nature of some examination approaches can lead to incongruities in assessments. Aesthetic evaluations may vary based on the inspector's experience and perspective.
Verdict
Welding assessment is necessary for preserving structural integrity and safety in numerous markets. Through the application of varied assessment techniques and adherence to established standards, examiners play a critical duty in making certain and determining problems conformity with market requirements. The difficulties faced in this area highlight the requirement for continuous renovation in evaluation techniques and practices. Inevitably, efficient welding inspection adds considerably to mitigating threats and boosting the general dependability of welded frameworks.
Welding inspection is a vital component in the building and construction and manufacturing industries, where the stability of bonded joints is critical to safety and dependability.Welding examination is important in making certain the integrity and security of welded frameworks, with researches suggesting that up to 70% of architectural failures can be traced back to insufficient welding methods. Their responsibilities encompass a detailed array of jobs, including visual evaluation of welds, examining welding documents, and performing non-destructive testing (NDT) approaches such as radiographic or ultrasonic screening to identify issues.
Welding examiners are also accountable for analyzing welding codes and criteria, ensuring that the welders are qualified and that the why not check here products used meet the required demands. Eventually, effective welding examination adds significantly to mitigating risks and enhancing the total integrity of bonded frameworks.